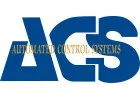
At safsale.com, we recognize that Automated Control Systems (ACS) play an increasingly vital role in the USA, driving efficiency, safety, and productivity across various industries. An Automated Control System is a combined set of technical and software tools intended for overseeing processes in manufacturing, production, or enterprise operations. Unlike fully automatic systems, ACS solutions rely on human involvement for decision-making, making them an ideal blend of human expertise and technological precision.
Below, we dive into the structure, key types, real-world examples, and future prospects of Automated Control Systems, demonstrating why they are a cornerstone of modern management and industrial processes.
1. Core Components of an Automated Control System
1.1 Technical Infrastructure
Hardware Components form the backbone of any ACS, including:
- Computers, Servers, and Network Devices: Provide the computing resources for data processing and inter-device communication.
- Sensors and Actuators: Continuously measure parameters (temperature, pressure, flow, etc.) and perform mechanical actions (valve control, motor speed adjustments).
- Display and Control Interfaces: HMIs (Human-Machine Interfaces), control panels, and other visualization tools that keep operators informed and enable direct interventions.
Given modern enterprise needs in the USA, these devices are typically designed to be modular. You can scale a system and replace individual modules—like upgrading a server or adding a specialized sensor—without performing a full system overhaul. This modular approach also ensures compliance with industry standards (e.g., ASTM, ANSI) while simplifying maintenance.
1.2 Software Components
Software within an ACS comprises both system-level and application-level layers:
- System Software: Governs basic computing tasks, networking, and resource management.
- Application Software: Encompasses databases, data management systems, specialized analytics solutions, and domain-specific programs (e.g., production scheduling, quality control algorithms).
Most cutting-edge ACS setups in the USA integrate advanced databases, real-time data analytics, and user-friendly development environments. This synergy maximizes control, enabling operators to make quick, data-driven decisions.
2. Key Types and Applications of Automated Control Systems
2.1 Process Control Systems (ACS TP)
ACS TP (Automated Control Systems for Technological Processes) target industrial processes—managing variables like temperature, pressure, and material flow rates. By automating the control loop around these parameters, an ACS TP:
- Reduces human-error risks,
- Ensures stable product quality,
- Minimizes resource consumption,
- Strengthens workplace safety.
These systems are ubiquitous in manufacturing across the USA—chemical plants, food processing lines, and heavy industry—where consistent product output and lower operational costs are paramount. They often incorporate robust control algorithms and safety redundancies to meet regulatory guidelines like OSHA or NFPA in the United States.
2.2 Enterprise-Level Control Systems (ACS UP)
ACS UP (Automated Control Systems for Enterprise Management) are comprehensive solutions that unify a company’s core operations:
- Production Management
- Supply Chain & Inventory
- Human Resources & Payroll
- Accounting & Finance
- Customer Relationship Management (CRM)
Often built on ERP (Enterprise Resource Planning) platforms, these systems enable real-time insights and resource optimization, crucial in a competitive USA market. Decision-makers can swiftly align production schedules with sales forecasts, ensuring lean operations and improved return on investment.
3. Real-World Implementation Examples
3.1 Industrial Production
In manufacturing (e.g., automotive plants), Automated Control Systems manage:
- Assembly Line Coordination: Real-time scheduling of tasks, controlling conveyor speeds, and orchestrating robotic welders or painting robots.
- Quality Assurance: Automated detection of defects, tracking production data to identify bottlenecks, and verifying that final products meet specification.
- Inventory and Supply Optimization: Minimizing overstock, ensuring just-in-time deliveries of materials to reduce costs.
Industrial sites in the USA rely heavily on these systems to reduce labor intensity and provide consistency. Operators, supervisors, and C-suite executives leverage data dashboards to maintain optimal throughput, making ACS solutions vital for sustaining world-class manufacturing standards.
3.2 Transportation Sector
The transportation industry benefits enormously from ACS technologies:
- Rail Networks: Synchronized train schedules, collision avoidance, remote monitoring of rolling stock, and predictive maintenance.
- Aviation: Advanced air traffic control systems ensure flight safety and efficient route planning in congested airspace.
- Metropolitan Subway Systems: Real-time train tracking, crowd management, and safety controls on escalators or platform gates.
Here in the USA, major cities adopt cutting-edge ACS solutions to optimize traffic flow, reduce delays, and enhance passenger experience. For instance, big data and AI-driven route planning can slash fuel consumption and streamline scheduling.
3.3 Energy Industry
The energy sector leverages ACS to handle electrical generation and distribution. Typical solutions involve:
- SCADA (Supervisory Control And Data Acquisition) systems: Enabling operators to monitor turbines, boilers, and ancillary equipment in power plants.
- Grid Management: Automated load balancing across states or regions, forecasting demand spikes, and adjusting supply accordingly.
- Renewable Integration: Seamlessly connecting solar and wind farms to the grid, dynamically handling fluctuations in generation.
In the USA, these advanced ACS solutions contribute to a more stable grid, higher efficiency, and better alignment with green energy targets.
4. Advantages of Production Automation
4.1 Economic Benefits
- Lower Operational Costs: Automated scheduling and resource allocation minimize unplanned downtimes.
- Reduced Waste and Defects: Systematic process control decreases scrap, improving yield.
- Faster Payback: Although an ACS implementation carries upfront costs, it’s usually offset by improved productivity and fewer mistakes caused by human error.
4.2 Technological and Operational Benefits
- Precision: Automated control loops and real-time data allow more accurate process adjustments than any manual approach.
- Reliability and Safety: Predictive maintenance features, built-in fault tolerance, and advanced analytics reduce risk of accidents or production halts.
- Scalability: ACS frameworks typically support a wide range of expansions, from additional sensors to entire production lines.
By harnessing the computing power and data analytics offered by modern technology, enterprises in the USA can remain competitive on both local and global stages.
5. Future Trends and Directions
5.1 Integration with Artificial Intelligence
Increasingly, automation merges with AI and machine learning. This synergy unlocks:
- Sophisticated Control Algorithms: Systems that autonomously adapt to changing conditions and produce recommendations.
- Pattern Recognition: AI helps identify operational inefficiencies and potential bottlenecks, guiding continuous improvement.
AI-driven ACS solutions can swiftly interpret data from a myriad of sensors, suggesting proactive maintenance or supply chain shifts. This dynamic approach is especially crucial in the fast-paced industries of the USA.
5.2 Industrial Internet of Things (IIoT) Adoption
Industrial IoT (IIoT) seamlessly integrates machinery, sensors, and cloud-based analytics, enabling:
- Remote Monitoring and Control: Real-time oversight of assets from any location.
- Predictive Maintenance: Algorithms that detect anomalies, schedule repairs, and avoid unplanned equipment breakdown.
- Enhanced Scalability: Adding or removing connected devices becomes easier.
As IIoT expands in the USA, ACS solutions become increasingly data-centric, bridging the gap between physical plant floors and digital management platforms.
Conclusion
Automated Control Systems have evolved into a crucial element of modern manufacturing, service industries, and enterprise operations. They empower organizations to reduce errors, streamline workflows, enhance safety, and boost profitability. At safsale.com, we’ve observed that synergy with AI, advanced analytics, and IIoT is pushing ACS technology to new frontiers—benefiting businesses of all sizes in the USA.
Embracing an Automated Control System is no longer optional for forward-thinking companies. With the proliferation of next-generation solutions, it’s evident that automation, analytics, and data-driven decision-making are vital to thriving in a competitive economy. Visit safsale.com today to explore how advanced ACS technology can revolutionize your operations, cut costs, and pave the way for sustainable, scalable growth.

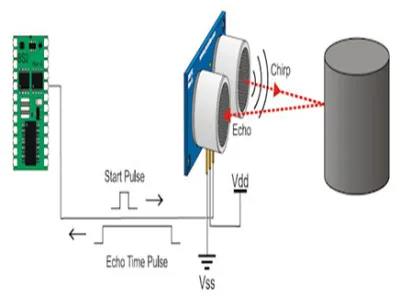
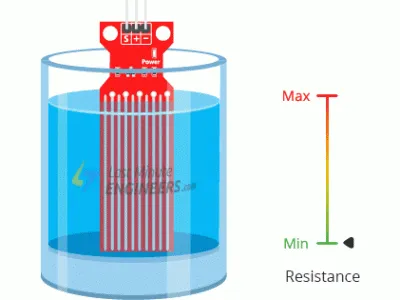
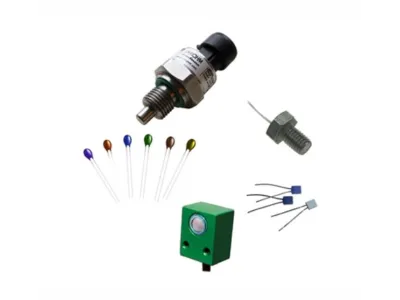
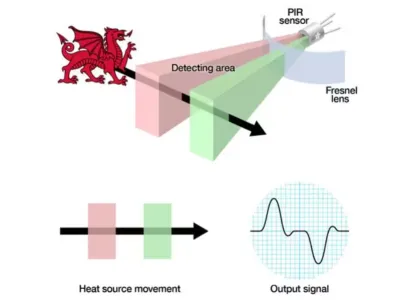
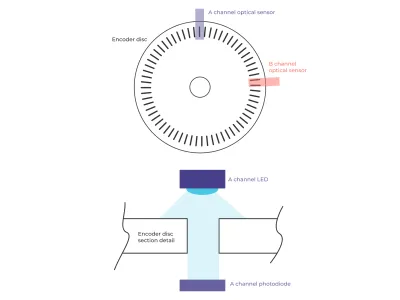
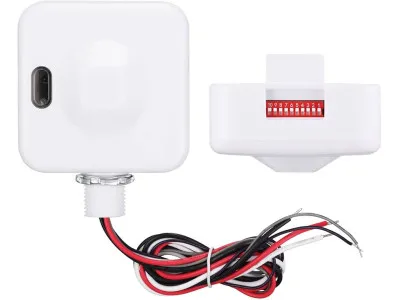
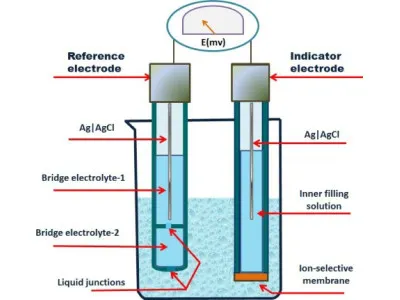
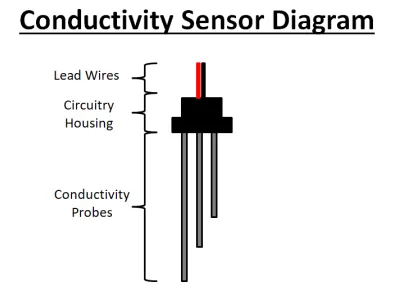

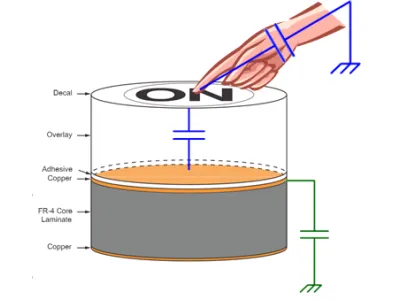
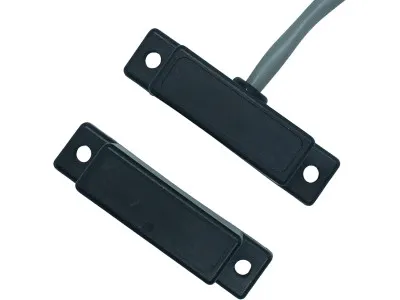
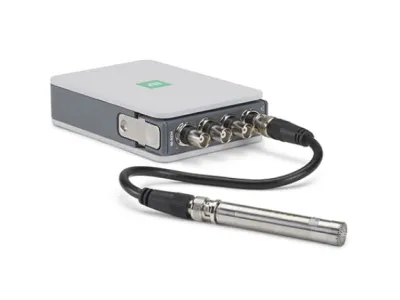
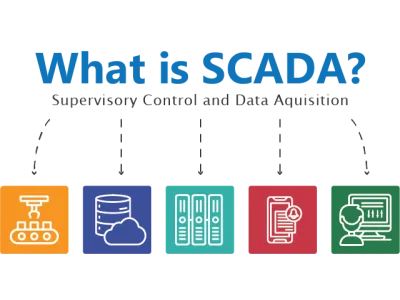

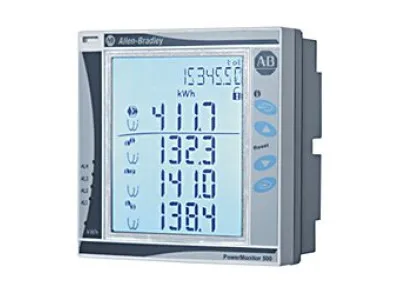